ワンオフ/ドレスアップ

くるま工房で実際にドレスアップした事例をご紹介します。
アルファロメオの中でも生産数が少ない、2ドアハッチバックのアルファロメオ ブレラです。


1.センターのマスキングテープから下の開口部を延長します。
プラスチック素材なため、歪んでしまう恐れがあります。なので、熱を加えながら地道に変形させていきます。
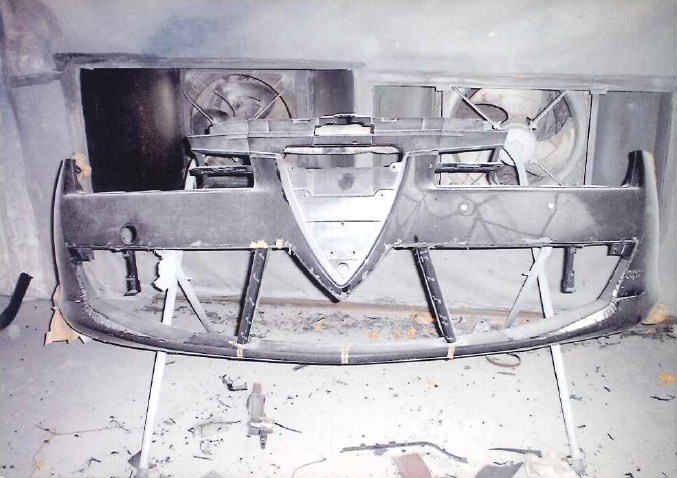
2.開口部がようやく理想の形となりました。中央にある2本の柱部分は元は厚みのある太い形でしたが、細いものに換え長さも延長し、開口部をより大きく見せ迫力を持たせるようにしました。

※試行錯誤を繰り返しながらのスポイラー製作でしたが、理想の形にすることができず自分自身妥協はできないので、他の方法に変更することにしました。
また、ワンオフ製作用の汎用品は多々ありますが、いずれもコストが掛かってしまいます。しかし、くるま工房ではリサイクルパーツを使用することによりコストダウンを実現しています。

4.今度は網目調のダクトを使用して形作りをしました。柔軟な素材のため、形作りが困難でした。なんとか仮止めまでできてホッとしました。

5.網目ダクトに発泡ウレタンを注入し形成を試みました。しかし、網目ダクトの強度が弱いために、ウレタンの硬化時に形が崩れてしまいました。また失敗となってしまいました。

6.また材料を変えてようやくスポイラー形成までに至りました。当然素材はプラスチック樹脂を使用しています。
残念ながら、プラスチック材料の詳細は企業秘密ですのでここではお見せできません。ちなみにこの材料は強度や柔軟性、密着性に優れており、どんなに曲げても折れることは絶対にありません。

7.サイドから見てバランスを確認しています。同時にスポイラーの出入り具合も確認しています。

8.サイドスリットは、バランスを見ながら3本入れました。スリット内側は細かい網目調のヨーロピアンネットを入れ、中が見えにくいようにしました。
ここで大体、作業は折り返し地点となりました。
部品製作において最も難易度が求められるのは、プラスチックパーツを左右対称に成形することです。寸法取りは板金用コンパス一本で全て行っています。

9.ようやく成形作業が終わり、柔軟性サフェイサーを塗って細かい部分のチェックをします。

10.アルファロメオの特徴であるフロントグリルです。純正ではメッキ調となっていますが、それではどうしても浮いてしまう印象があります。なのでここは、後で塗装するためにオリジナル製作しました。
11.ボンネットエンブレム部分にもメッキが使用されていたので、それを取り除きボンネット先端を自然なラインに延長し、一体化させ成形しました。

12.フォグランプのグリルカバーです。この部分だけはFRPで成形しました。裏側にボルトを固定し、脱着可能にしました。
(FRPはプラスチック樹脂に比べ成形が容易で、作業性が良いのが特徴です。)

13.ようやく、全ての制作過程が終了しました。上下左右のバランス、面だしは理想通りの仕上がりで満足しています。

14.バンパーの塗装工程です。凹凸部分が多く、気を遣いながらのスプレー仕上げが必要とされます。当然全ての箇所を、同じ膜厚でフルウェットにします。こうすることによって後々にワックスをかけやすく、磨きやすい状態を保つことができます。
15.最終、ボンネットの塗装です。側面と違い平面部分に関しては、均等な塗膜の厚さと強度が求められます。ボンネットはエンジンの熱や紫外線、酸性雨に影響されやすい場所であり、それに対抗できる性能を持つクリア樹脂塗料が必要とされます。
くるま工房はスタンドックス マイスターワランティ認定工場であり、塗装後4年半の保証とともにお客様に安心を提供させていただいています。
16.これがアルファロメオ ブレラの完成した姿です。
あなたも、世界に一台だけのオンリーカーを作ってみませんか。